Injection moulds are curious machines. They are the basis for one of the most efficient and widespread manufacturing processes ever devised. They create parts with such speed and repeatability that we can’t help but take their output for granted. They are so effective that it’s easy to judge them in the same way we judge their output. Cheap, easy and plentiful plastic components surround us, so injection moulds must be cheap and plentiful too, right?
Nothing could be further from the truth. For every ubiquitous plastic product there lurks at least one (and possibly a family of) highly complex, custom made, hand fitted masterpieces of metal fabrication and polymer knowledge.
Each injection mould has to be designed to not just reliably produce a part, but to do so in a way that matches the production needs of its owner. They must balance production speed, mechanical reliability and physical size. They must possess sufficient longevity, be capable of future modification, and fit in an almost unlimited array of injection moulding machines.
Above all, they must be a worthwhile investment. Nobody makes anything by the thousands just for the hell of it. Injection moulds are there to make a profit.
In this series we are going to dive into an array of injection moulds. There are a lot of technical details, but the bottom line is always the same. Each tool is the result of a series of choices. Each of those choices will affect your bottom line. Let’s jump in and look at the choices some others have made, and their consequences.
The nutcracker suite
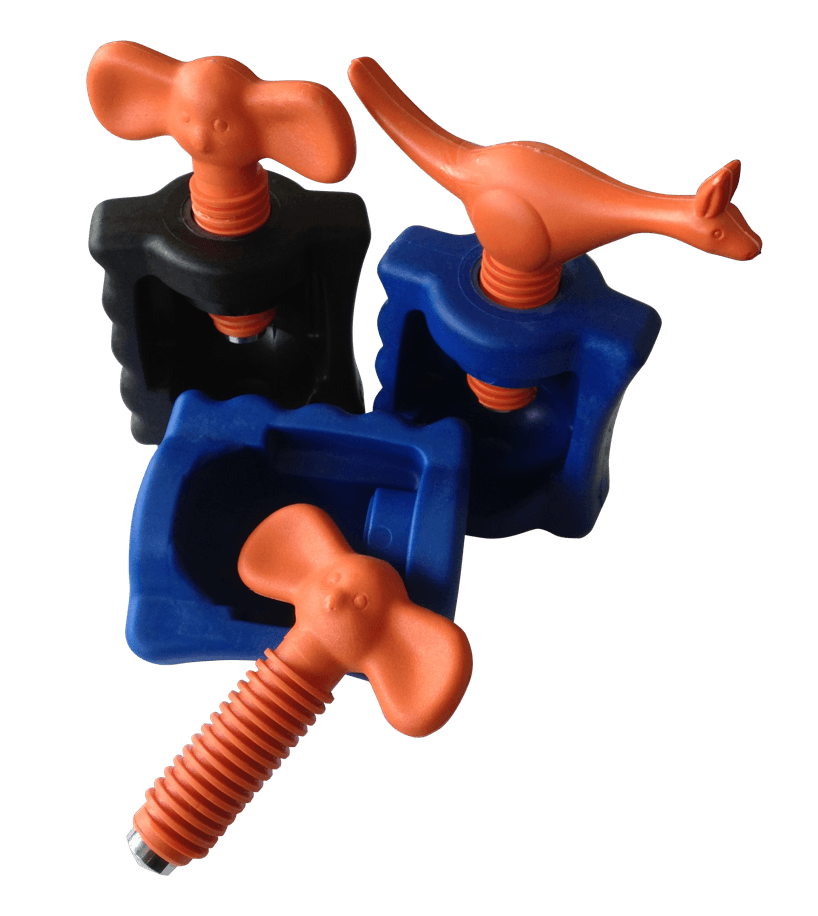
(The finished product)
Welcome to the land of novelty nutcrackers. As a quick perusal of any bargain store shelf will tell you, novelty items are not normally built to last and are priced accordingly. Nutcrackers, on the other hand, have to apply quite a bit of force to actually crack a nut, especially in macadamia happy areas.
This leads to an immediate conundrum. How to get a very stout part for cheap?
The part in question took the brute force approach. It’s simple, heavy and hard to break. It’s also really hard to mould and prone to quality control issues. We have covered design approaches like nominal wall section and draft in previous articles, so for now we are going to focus on the tool that was designed around this monster. As we go through, bear in mind the part and tool design go hand in hand. Each design has to take account of the needs of the other, and any change to one will affect how the other functions.
The choices
Cost
Injection moulds are a substantial investment. You need to build them in order to make the part, so it’s also an investment you have to make up front, before you get the opportunity to start making revenue on the product.
Because of this, they are always costs sensitive. There is no such thing as a “money no object” project, and anyone who thinks otherwise will soon find they cannot make the object they need to, because they have no money.
In order to control investment cost this tool was built off shore by the lowest bidder. The quality of the resulting tool reflected that.
This brings up a simple rule – In manufacturing, no matter what you are making or where you are making it, you will always get what you pay for. Off shore may look like the best option at first glance, but sharks swim in those waters, and they are ready to take a bite out of you bottom line.
By going for the cheapest option the history of this tool was set. Sure, the initial cost was low, but this manufacturer was not responsible for the problems caused by corner cutting down the line. As such they gave no warning about design flaws that would lead to QC issues and reject parts, and did not consider the actual end cost of the parts.
Labour
Injection moulding gets a large part of is cost effectiveness from its ability to reduce labour costs. Properly set up tools should work with minimal human intervention, eating plastic and ejecting finished parts automatically. This is not the case here. Key automation features were not designed into the tool, requiring an operator to be on hand to ensure it kept running. Not only must those operators’ costs be built into the final part cost, they also slow down production.
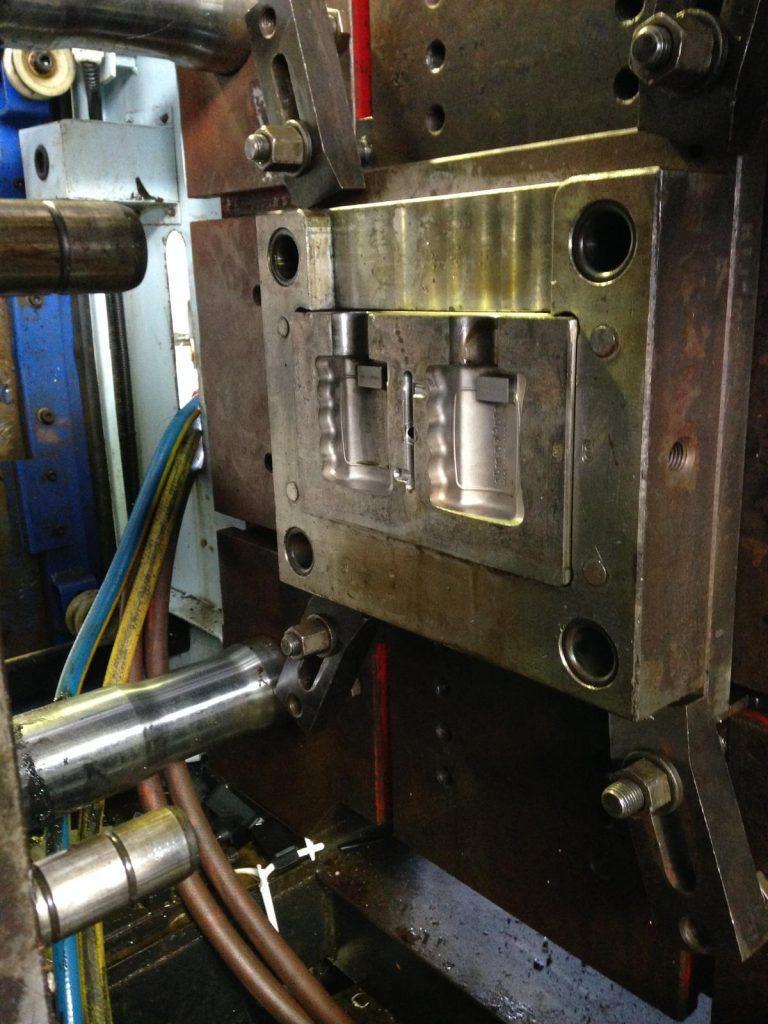
(Nutcracker tool built by Dienamics)
Tools that can run unattended do not care about the opening and closing hours of the factory they are in. Once set up, they will keep on running so long as there is plastic. If an operator is required, they are now locked to the shifts of the factory, which may not run 24/7. This means the tool will have to be shut down and restarted daily, and can add days to the time required to produce any given number of parts.
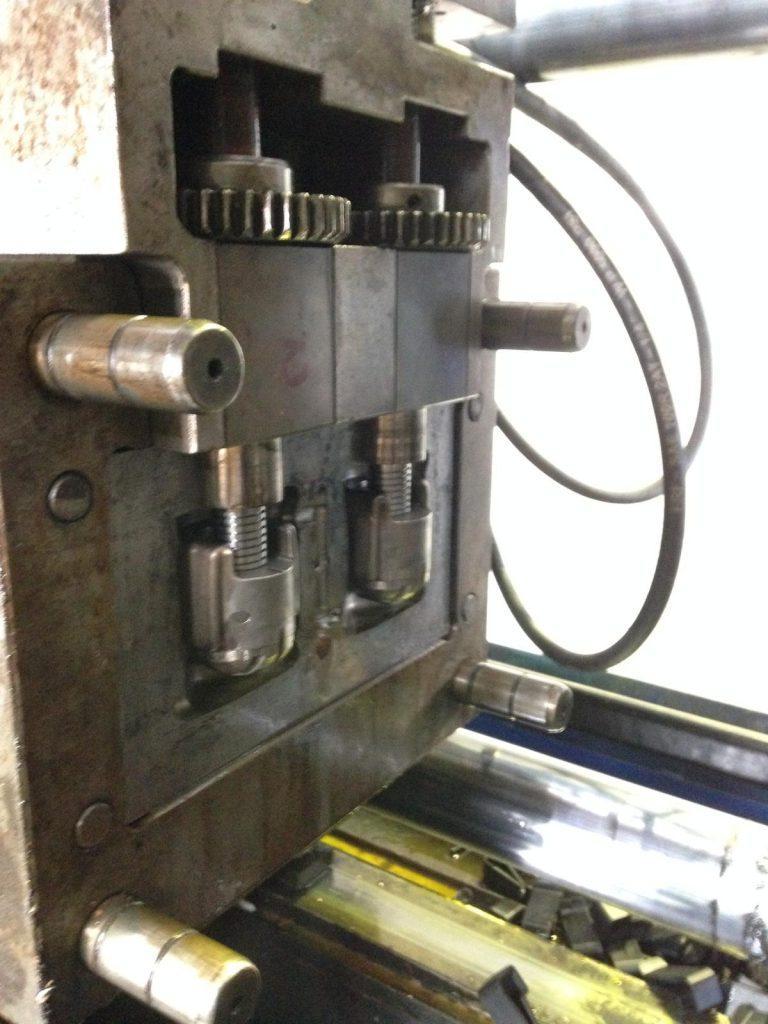
(Nutcracker tool built by Dienamics)
Location, location, location
Injection moulding machines are fairly similar the world over. However things like electrical connections vary country to country. The manufacturer of this tool built it to their own countries standards, even though the plan was always for the tool to be run in Australia. This necessitated significant electrical refit work once it landed down under.
Maintenance
Simply put, in the interests of cost this tool was not built to be easily taken apart. Many parts of an injection moulding tools are custom made, and good tool makers will ensure that parts likely to wear or break are isolated and easily removable. This is so that when they wear out, only the minimal amount of work is needed to make a new part and fit it. This principle was not followed here, probably in the interests of saving time. The upshot is large upkeep costs, as every time a small feature breaks, whole sections of the tool need to be replaced.
In a catch 22 for the client, their product has proven quite popular. They have not been able to see the profits they would have liked due to that popularity, as simply keeping the tool running is a serious financial burden.
Adaptability
Products evolve. Many times small adjustments can be made to a tool over its life to update the product, or address issues that only became apparent when the product was being used by a wide audience. The same issues that affect maintenance strike here.
Nothing in this tool is simple to access, and many of the initial tooling design choices have led to parts that cannot be changed without replacing several other parts as well. Better design would have taken account of possible changes from the outset, making a few parts more expensive initially in order to reap considerable savings later on in the tools life.
Subscribe to Our Newsletter
Get the latest news from Dienamics into your inbox