In Issue 5, we looked at SLS 3D Printing, and in Issue 7, we covered both SLA and FDM 3D printing. All of these 3D printing, prototyping, or model-making processes are classified as ‘additive manufacturing.’ In this issue, we’ll look at the opposite, ‘subtractive manufacturing’ process of CNC machining.
Using 3D CAD data, a CNC machine forms a product by using a number of different sized and shaped spindle cutting tools to ‘subtract’ material away from a material block (See. Image 1).
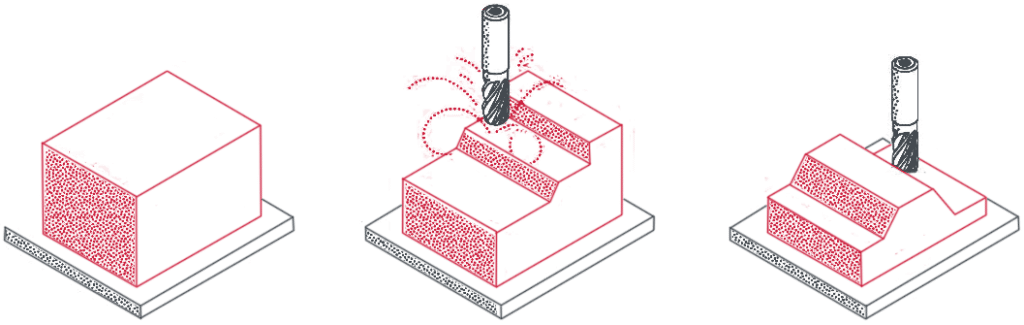
Image 1: CNC Machining Subtractive Manufacturing Process
Pro’s
If you’re looking to create a functional prototype, CNC’ing is a great option. CNC’ing outperforms the accuracy of any 3D printing process:
- It is a lot more accurate;
- CNC’d parts have a much better finish and if they’re made from harder plastics, they can also be polished to a high gloss;
- Most CNC plastics can be painted, in some cases producing a finish that is better than an injection moulded part;
- Because the design can be CNC’d in the plastic it will be injection moulded from, CNC’d prototypes are great for physical testing and getting a true feel for what the final product will be like; and
- In some cases it can be as cheap as, or cheaper than 3D printed parts.
Con’s
- CNC machines use cutters, alike drill bits, which are round – this means that internal corners will be radiused/rounded; and
- It can be issue if the design has fine details at the bottom of deep pockets – this is because small cutters (1 or 2mm) are required to achieve fine detail. If the detail is at the bottom of a 50mm deep pocket, it couldn’t be done as you can’t get cutters that small in that length. There is relationship between the diameter and length of cutters that are available.
- A lot of the time this isn’t an issue as segments of a design can be CNC’d separately and glued together after;
- It is only an issue if the material slab available isn’t long/wide enough or it isn’t thick enough – which is rare; and
- Sometimes prototypes will have segments CNC’d separately and glued if the part is too hard to machine, and it makes more sense ‘split and glue’ it.
To summarise, we highly recommend prototyping using CNC machining. This is because it is accurate, offers many materials to choose from, is cost efficient, and produces prototypes that look like final injection moulded parts. We would do more of these prototypes than any other
Time
CNC’d prototypes have an approximate lead time of 2 weeks. Generally, CNC’ing is quicker than Vac-Casting, but not as quick as some types of 3D printing.
Subscribe to Our Newsletter
Get the latest news from Dienamics into your inbox